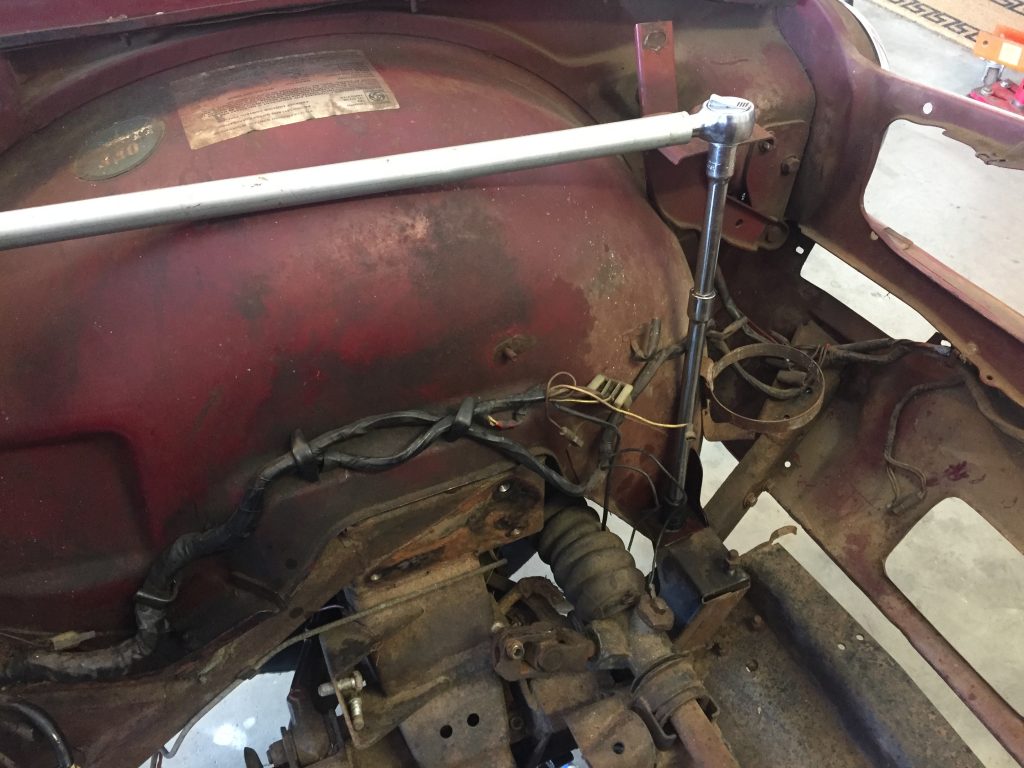
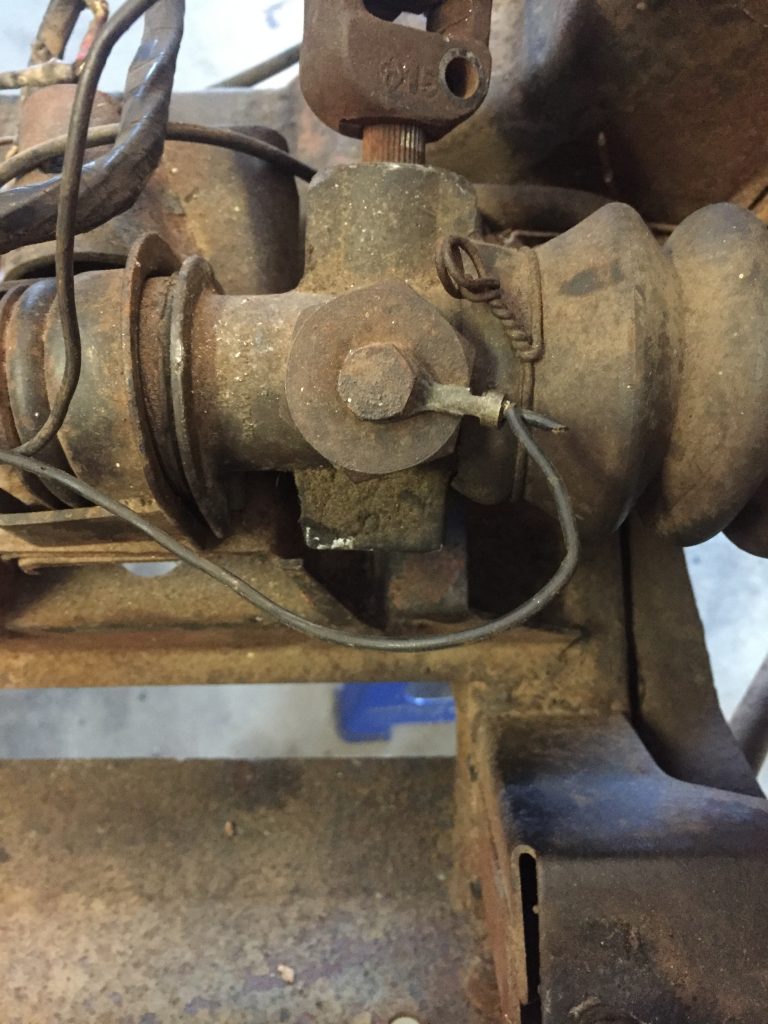
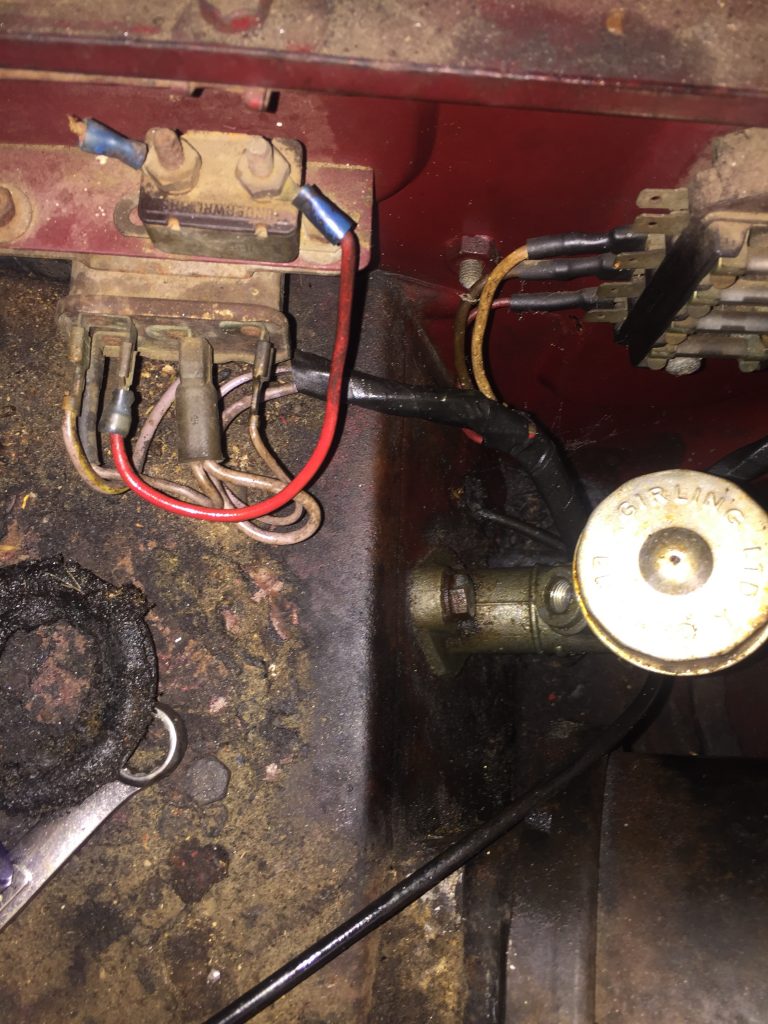
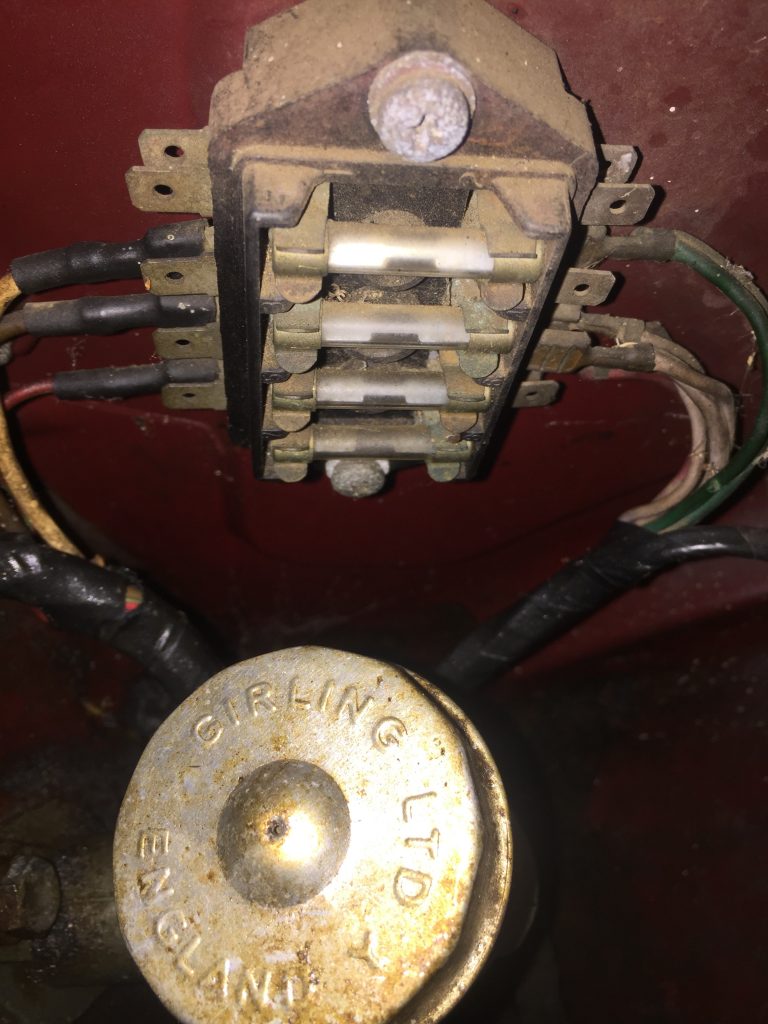
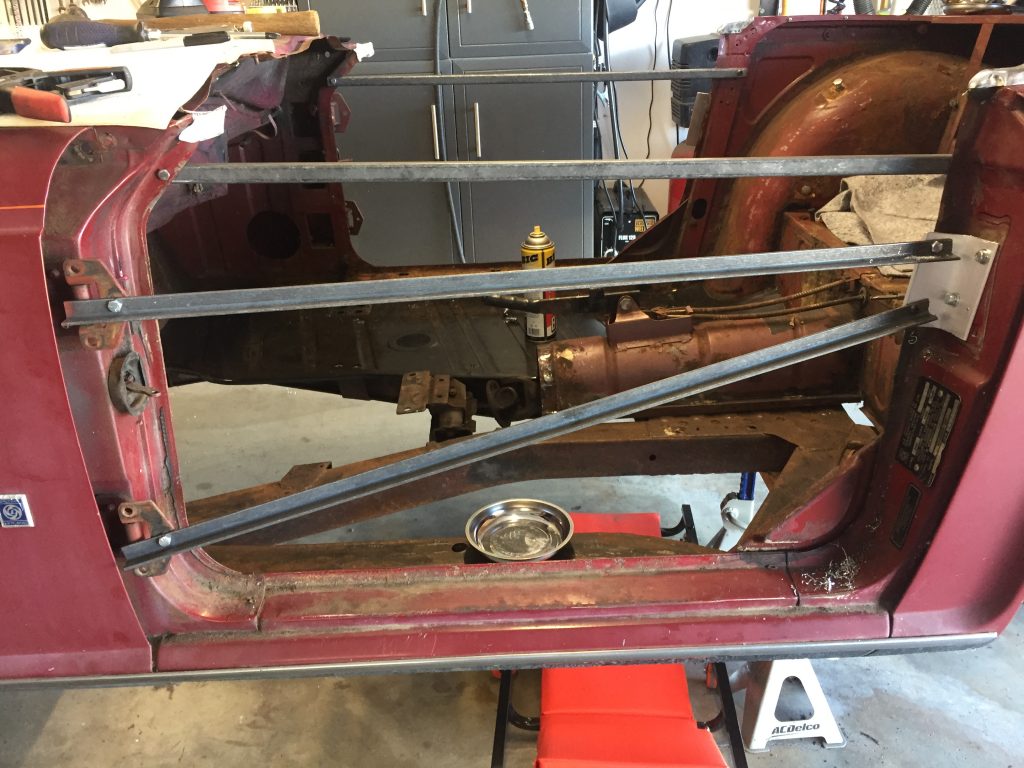
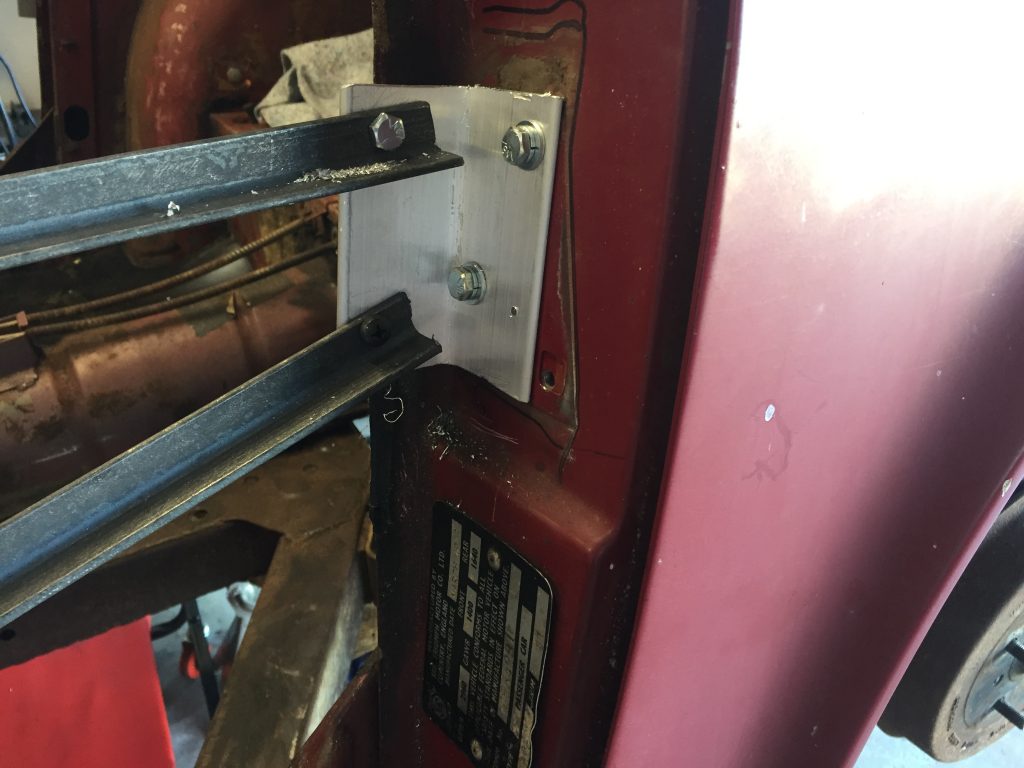
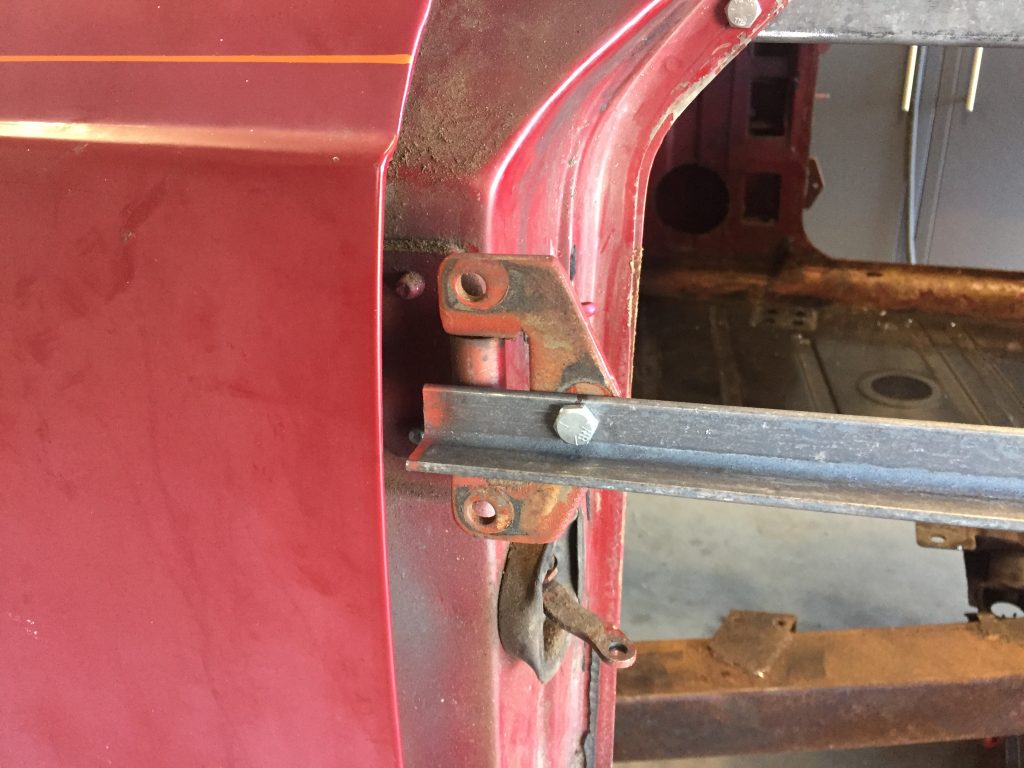
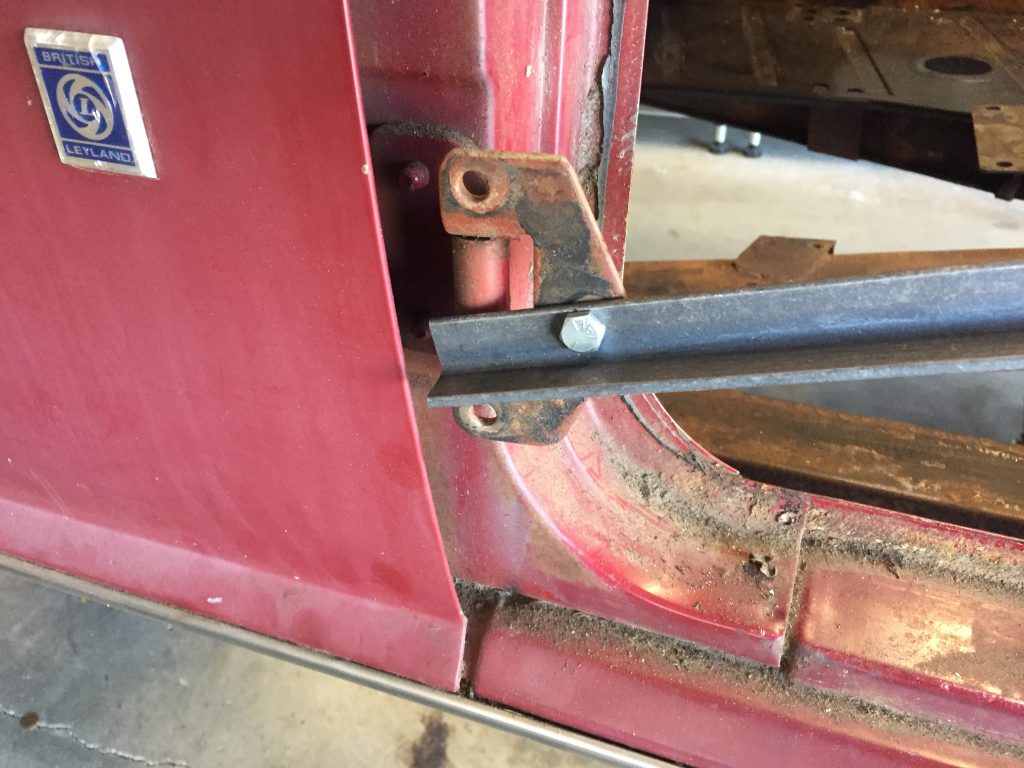
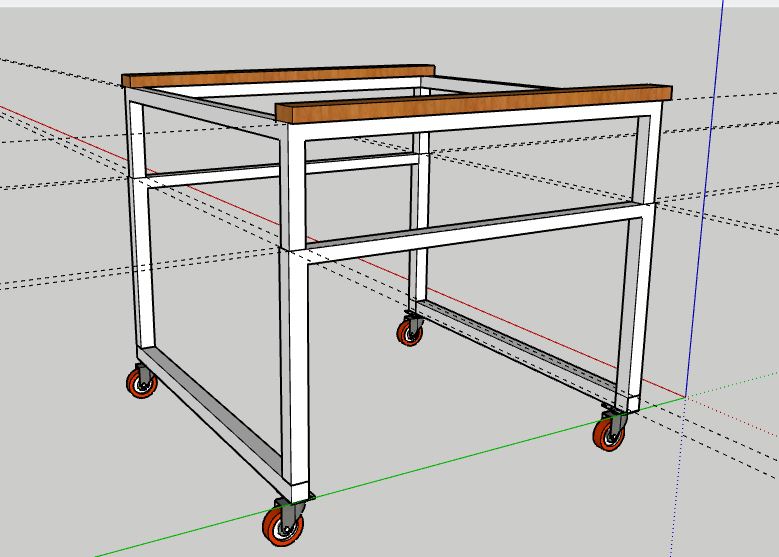
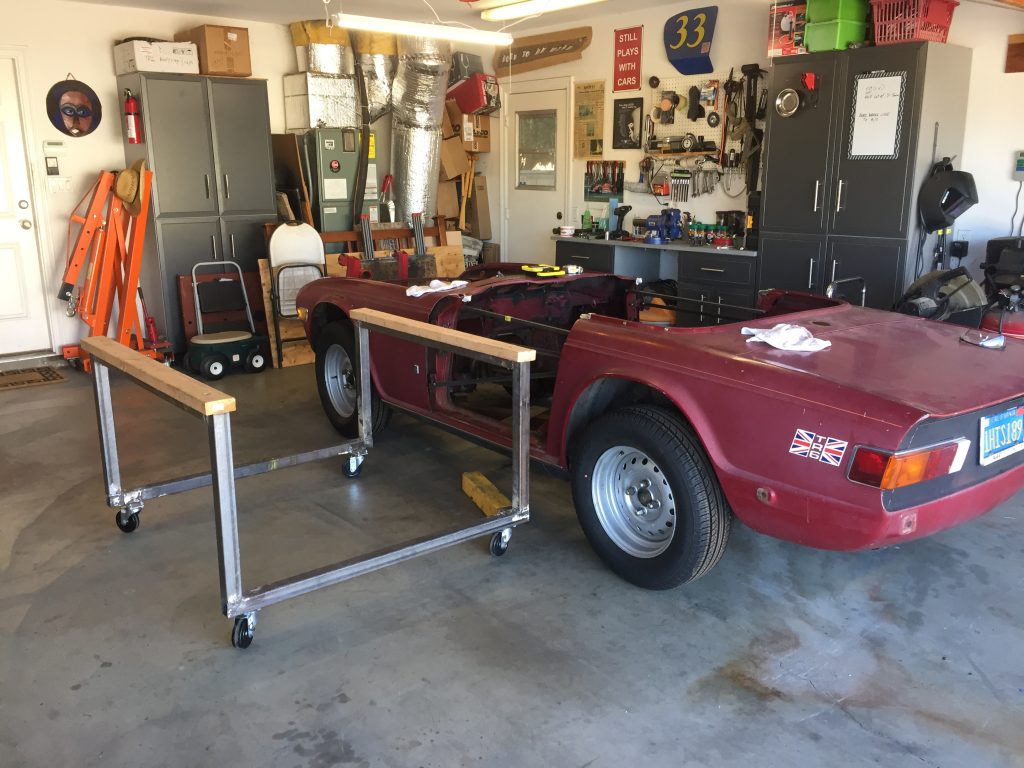
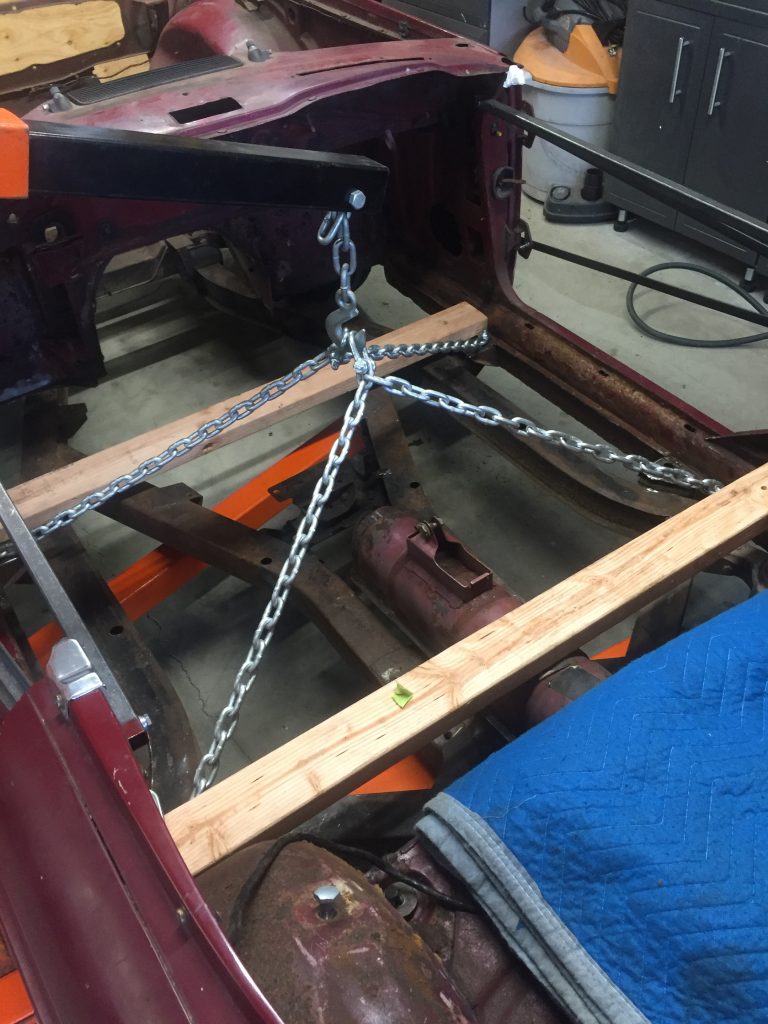
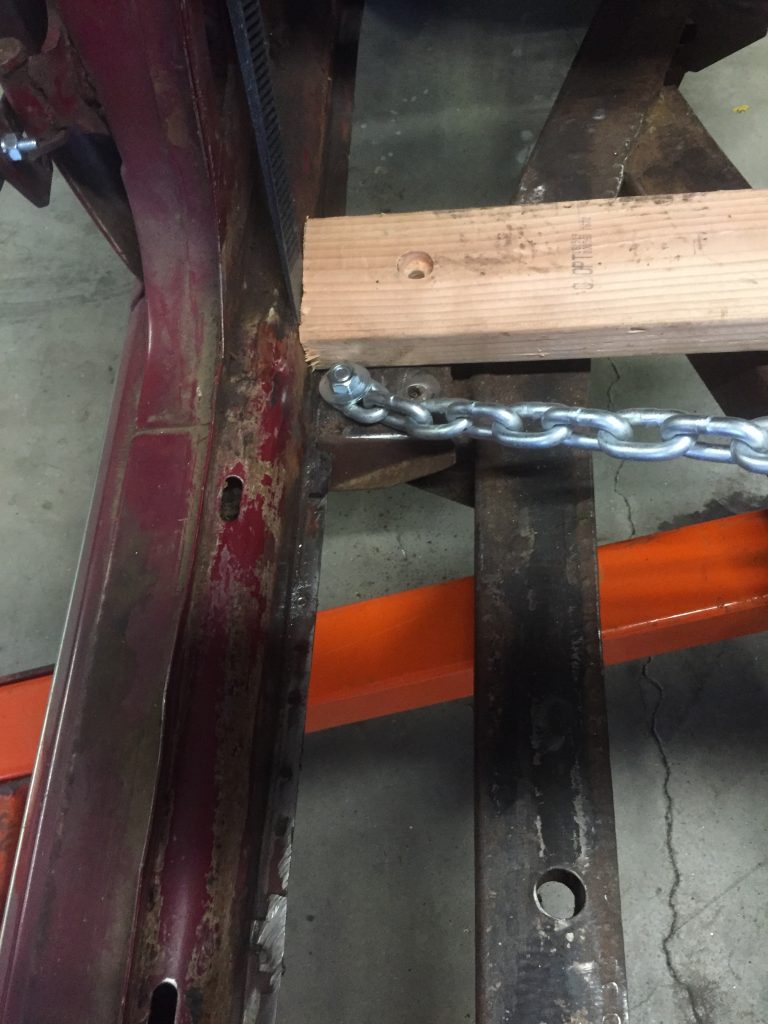
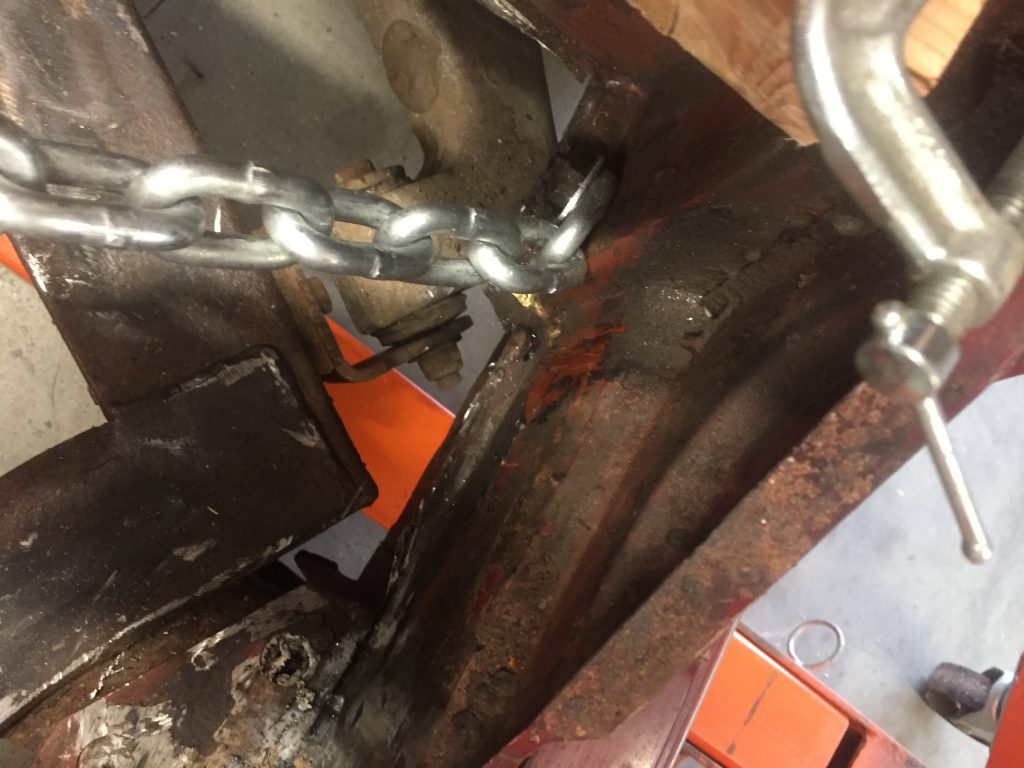
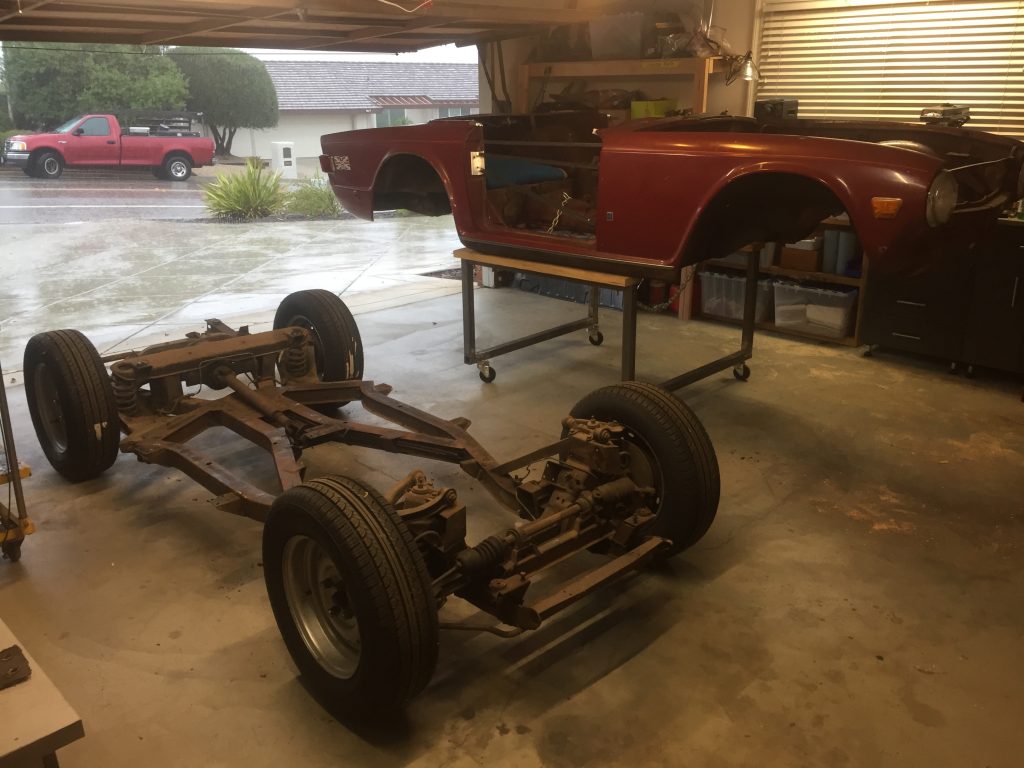
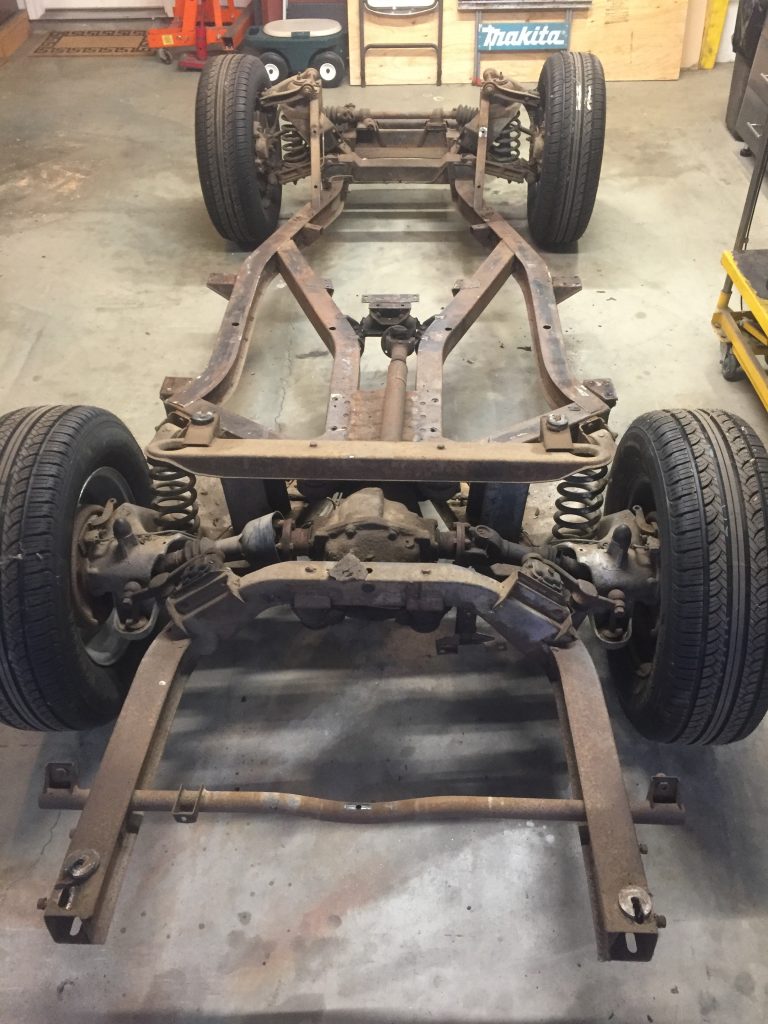
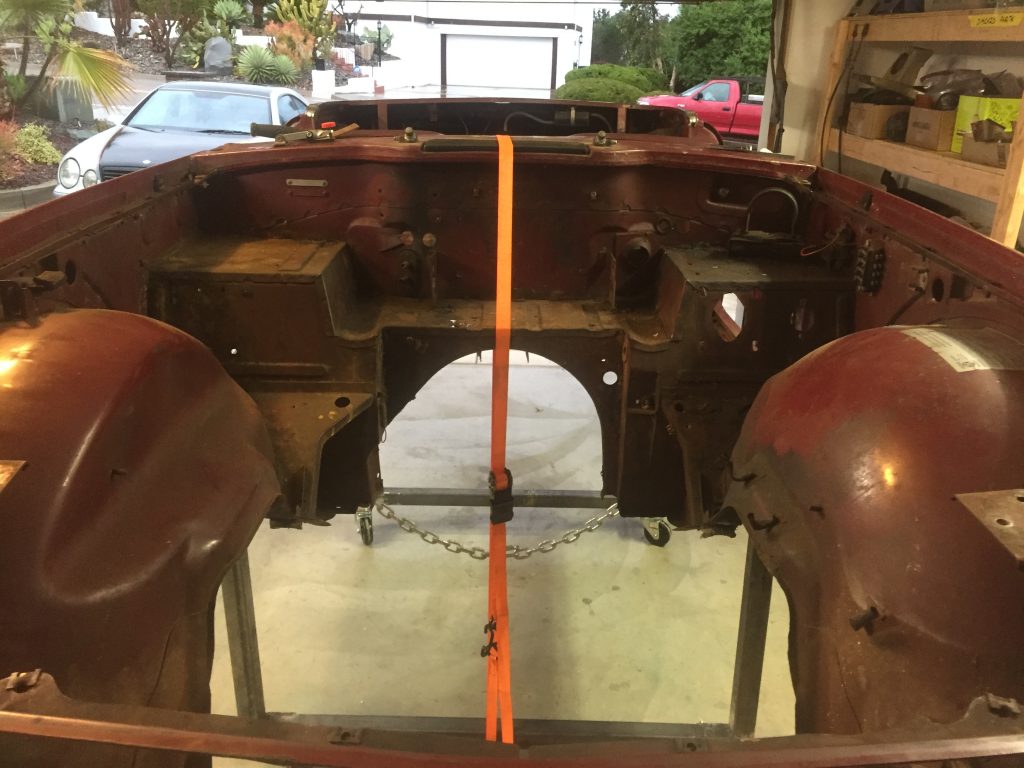
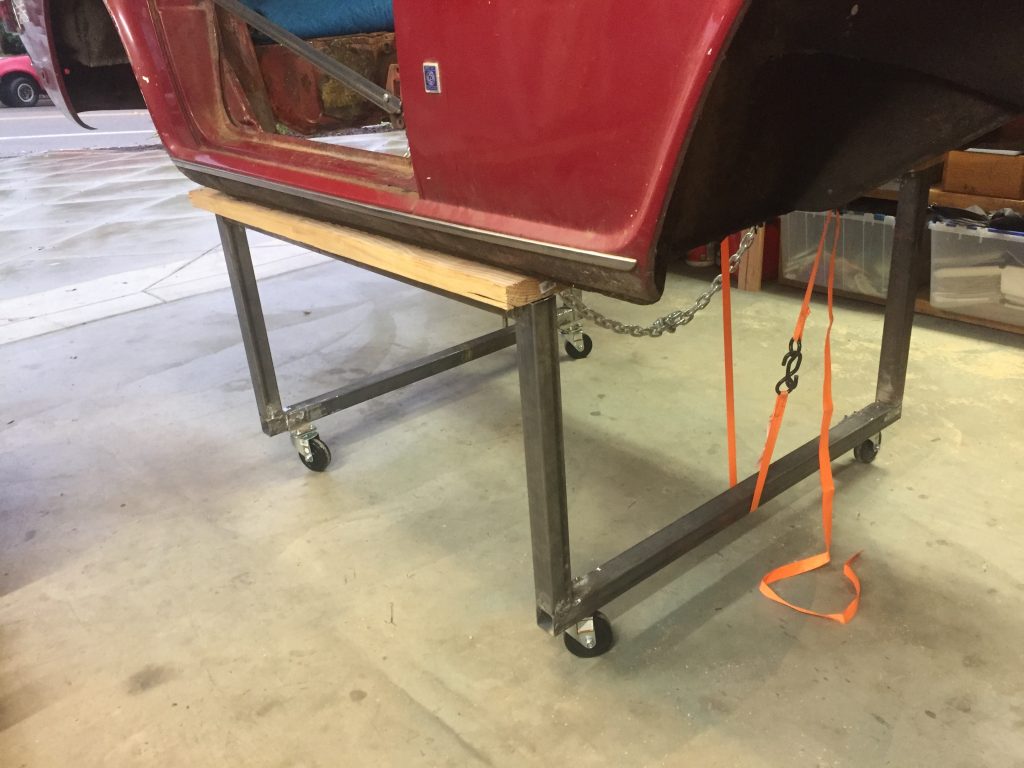
Separating the body from the chassis was a momentous occasion, and pretty straightforward, with the engine and transmission and the passenger floors and gas tank already removed. One of the online sites, can’t remember whether it is TRF or Moss, has a good illustration of all the bolts securing the body, and that was helpful for removal and re-assembly. Of course there are brake lines and fuel lines and other bits that need to be undone, as well.
We used our engine hoist to do the lifting, anchoring the chains as shown in the photos. I built a stand with wheels so that the body could be moved around in the garage. The stand also allowed me to work while standing up inside the engine bay or passenger area when necessary. As you can see in the pictures, I utilized the door hinges and latch holes, along with a couple other existing holes, to brace the body so it would not fold and create problems later. I really didn’t want to go to the trouble of welding and and then grinding off the braces, nor did I want to drill any holes.